Recyclen van composietmateriaal, zónder handwerk
Ilse ten Bruggencate, onderzoeker Lichtgewicht Construeren, boog zich met een creatieve groep studenten over de optimalisatie van het recycleproces voor Long Fiber Thermoplastic (LFT). Een verhaal over duurzame composieten en de helpende hand van een robotgrijparm. Ofwel: de LFT handling tool. “De productie van onderdelen, bijvoorbeeld voor de vliegtuigindustrie, kan tot wel 30% afvalmateriaal opleveren. Hartstikke zonde van de grondstoffen, en een verspilling van geld. Maar ook aantrekkelijk voor innovatieve afnemers.”
Bij TPAC, het ThermoPlastic composites Application Center in Enschede, richten onderzoekers zich op het produceren met thermoplastische composieten. Denk hierbij bijvoorbeeld aan duurzaam plaatmateriaal. Binnen de onderzoekslijn Recycling is de centrale vraag hoe je een recyclingproces zo hoogwaardig mogelijk kunt inrichten. “Hoe kun je nou zoveel mogelijk waarde van materiaal behouden als je het gaat hergebruiken?” vraagt Ilse ten Bruggencate zich hardop af. “Zes jaar geleden hadden we een eerste project rondom die uitdaging. In dat project hebben we het LFT-recyclingproces ontwikkeld. De werking van dat proces hebben we vervolgens aangetoond door het maken van enkele vliegende onderdelen. Toen zeiden we tegen elkaar: hoe nu verder? Vanuit die vraag is het project met de LFT handling tool ontstaan. Nu kijken we vooral naar de mogelijkheden voor industrialisatie.”
Simpel gezegd gaat het bij de LFT handling tool om een apparaat dat ‘vers gesmolten’ afvalmateriaal nauwkeurig verplaatst tussen twee stappen in het recycleproces, waarbij er niks verloren mag gaan of vervormd mag worden. Stel je letterlijk een robotgrijparm voor die het nog warme materiaal vastpakt met een soort ‘naaldvingers’, om het vervolgens door te geven aan een machine die er een product van perst in een mal. “Voor het project hebben we een recycleproces ingericht op batch-schaal,” legt Ilse verder uit. “Dat zijn we nu aan het opschalen naar industrieel niveau. We moeten toe naar een proces met zo min mogelijk menselijke handelingen. Waarbij het verplaatsen van materialen die gemixt en verwarmd zijn dus een van de uitdagingen is.”
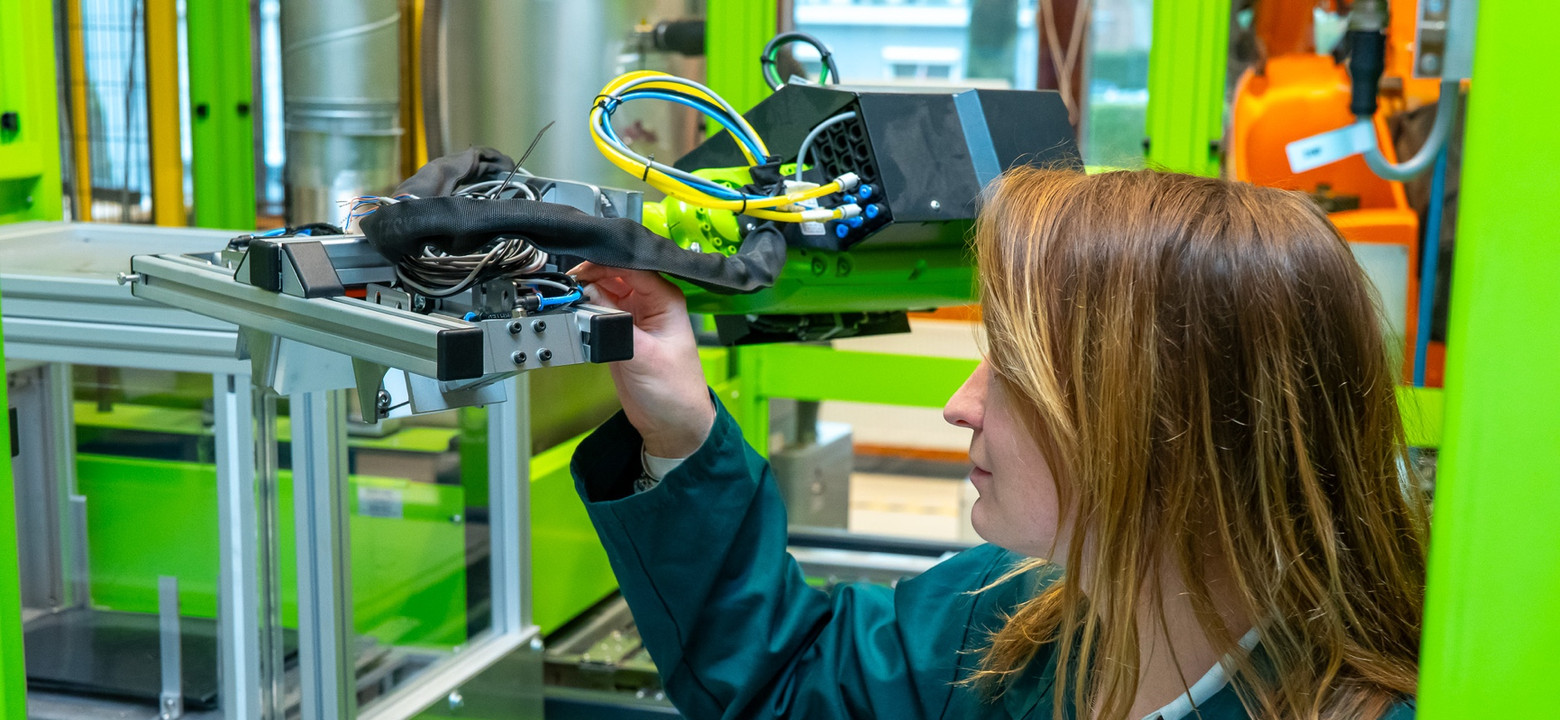
Ilse ten Bruggencate bij de LFT handling tool.
Vliegtuigonderdelen
Thermoplastisch composietmateriaal kan relatief eenvoudig worden omgesmolten, en is daarmee uitermate geschikt voor recycling. “Op grote schaal gebeurt dat alleen nog niet zoveel,” zegt Ilse. Wie zeker baat kunnen hebben bij recycling van thermoplastisch composietmateriaal op grotere schaal, zijn de praktijkpartners die waren aangehaakt bij het project rondom de LFT handling tool.
“In dit project hebben we samengewerkt met Toray Advanced Composites,” vertelt Ilse, “een materiaalleverancier in Nijverdal. Het plaatmateriaal dat zij maken, gaat vervolgens naar Collins Aerospace in Almere. Daar wordt het plaatmateriaal weer gebruikt voor het maken van producten, die zijn ontworpen door GKN Fokker. Denk hierbij aan onderdelen voor vliegtuigen van Boeing of Airbus.” Zowel met Toray, Collins Aeropspace als GKN Fokker heeft TPAC al vaker samengewerkt. “Eigenlijk hebben ze allemaal interesse in het recycleproces waarmee we ons tijdens het project hebben beziggehouden,” vervolgt Ilse. “De ene partij maakt het materiaal, de andere verwerkt het, en de afvalstroom die daarbij vrijkomt is waar wij binnen ons project naar hebben gekeken.”
Uiteindelijk wil je naar end of life-materiaal. Denk aan een vliegtuig dat tientallen jaren heeft gevlogen: ook dan wil je het ‘trucje’ van het recyclen nog kunnen toepassen.
End of life materiaal
Een recycleproces voor materiaal dat uiteindelijk zelfs in nieuwe vliegtuigen kan worden verwerkt: het prikkelt de fantasie. Zou je het LFT-recycleproces in theorie ooit kunnen starten met een ontmanteld vliegtuig? “Dat zal ons einddoel zijn,” zegt Ilse. “We werken nu dus met productieafval. Je moet je voorstellen dat een partij als Toray eerst een grote plaat maakt. Daar worden allemaal vormen uitgesneden, en dan blijft alleen het ‘geraamte’ van die plaat nog over. Maar daarbij gaat het gewoon om kostbaar, hoogwaardig materiaal. Waar dat voorheen werd weggegooid, wordt het nu door ons verzameld. Daarna shredden we het materiaal en recyclen we het volgens ons proces.”
Momenteel kunnen van het door TPAC gerecyclede materiaal nog geen dragende onderdelen worden gemaakt, bijvoorbeeld weer voor vliegtuigen. “Dat is echt nog wel een stap verder,” zegt Ilse. Voorbeelden van producten die al wel van gerecycled composietmateriaal kunnen worden gemaakt, zijn luiken of afdekkapjes. “Uiteindelijk wil je naar end of life-materiaal. Denk aan een vliegtuig dat tientallen jaren heeft gevlogen: ook dan wil je het ‘trucje’ van het recyclen nog kunnen toepassen.”
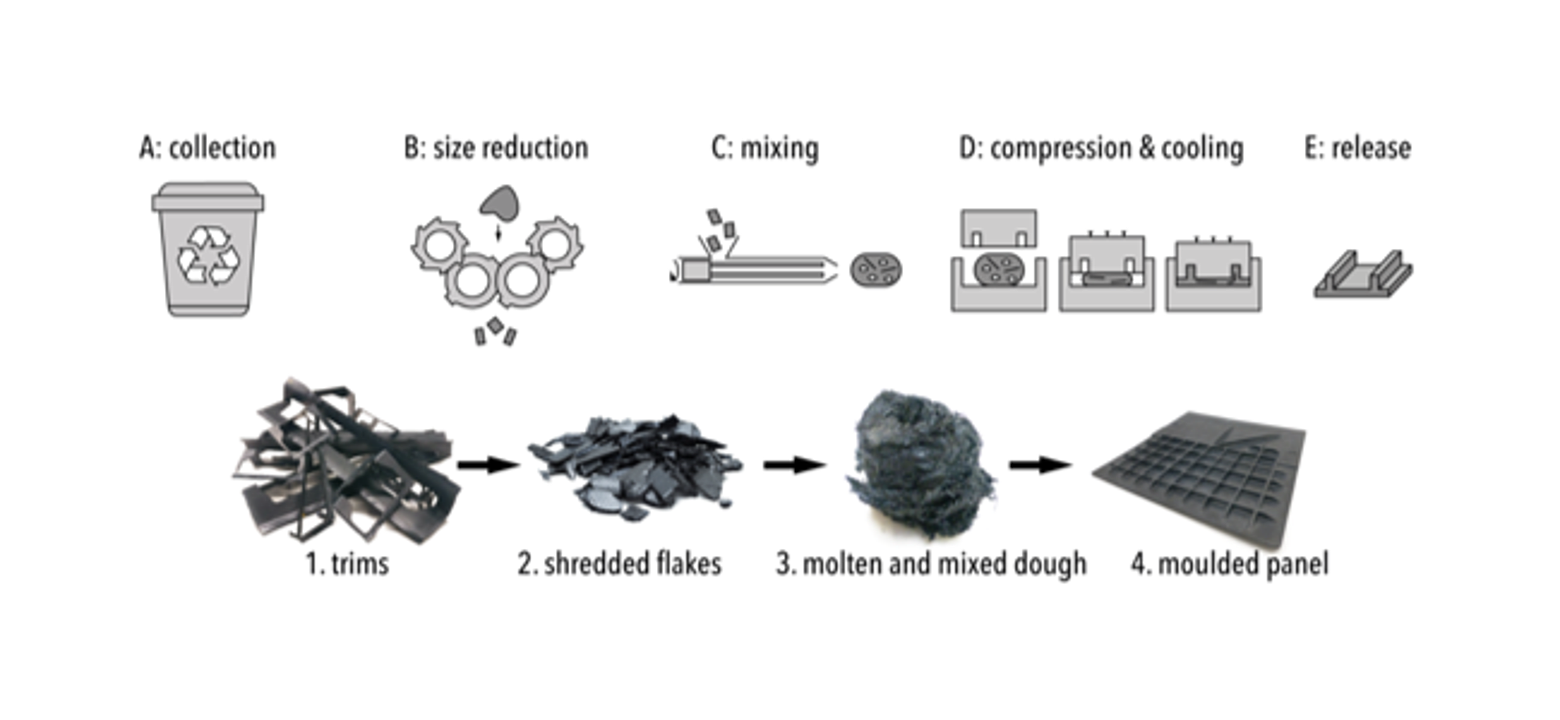
Het recycleproces schematisch in beeld (de LFT handling tool komt tussen stappen C en D in actie).
Zoeken naar het optimale proces
Hoe puurder een materiaal, hoe beter geschikt voor recycling. Om die reden wordt er in het project ook gekeken naar het effect van vervuiling. Zo wordt er aan sommige vliegtuigmaterialen een laagje kopergaas toegevoegd dat bescherming biedt tegen blikseminslag. Een vraag is dan bijvoorbeeld of de eigenschappen van het materiaal achteruitgaan als deze beschermlaag meegaat in het recycleproces?
Een ander vraagstuk heeft veel met duurzaamheid te maken. In een ideale situatie zou productieafval op locatie gerecycled kunnen worden. Zodat het vervoeren van afvalmateriaal – wat zorgt voor CO2-uitstoot – niet meer nodig is. Wetgeving speelt in dit verband een belangrijke rol. Want wie is er bijvoorbeeld verantwoordelijk voor een afgedankt vliegtuig? Is dat de producent, de eigenaar of een andere partij? Ilse reageert: “Daarom is het juist zo mooi dat we nu met drie partijen aan tafel zitten die allemaal interesse hebben in een optimaal proces. En ook in de vraag wie er verantwoordelijk zijn voor de verschillende procesonderdelen. Aantonen wat de voordelen van zo’n geoptimaliseerd proces zijn is de eerste stap. Daarmee schep je vertrouwen. Daarna kun je verder kijken: misschien is er wel een nieuw bedrijf nodig in de keten, bijvoorbeeld voor het verzámelen van al dat productieafval?”
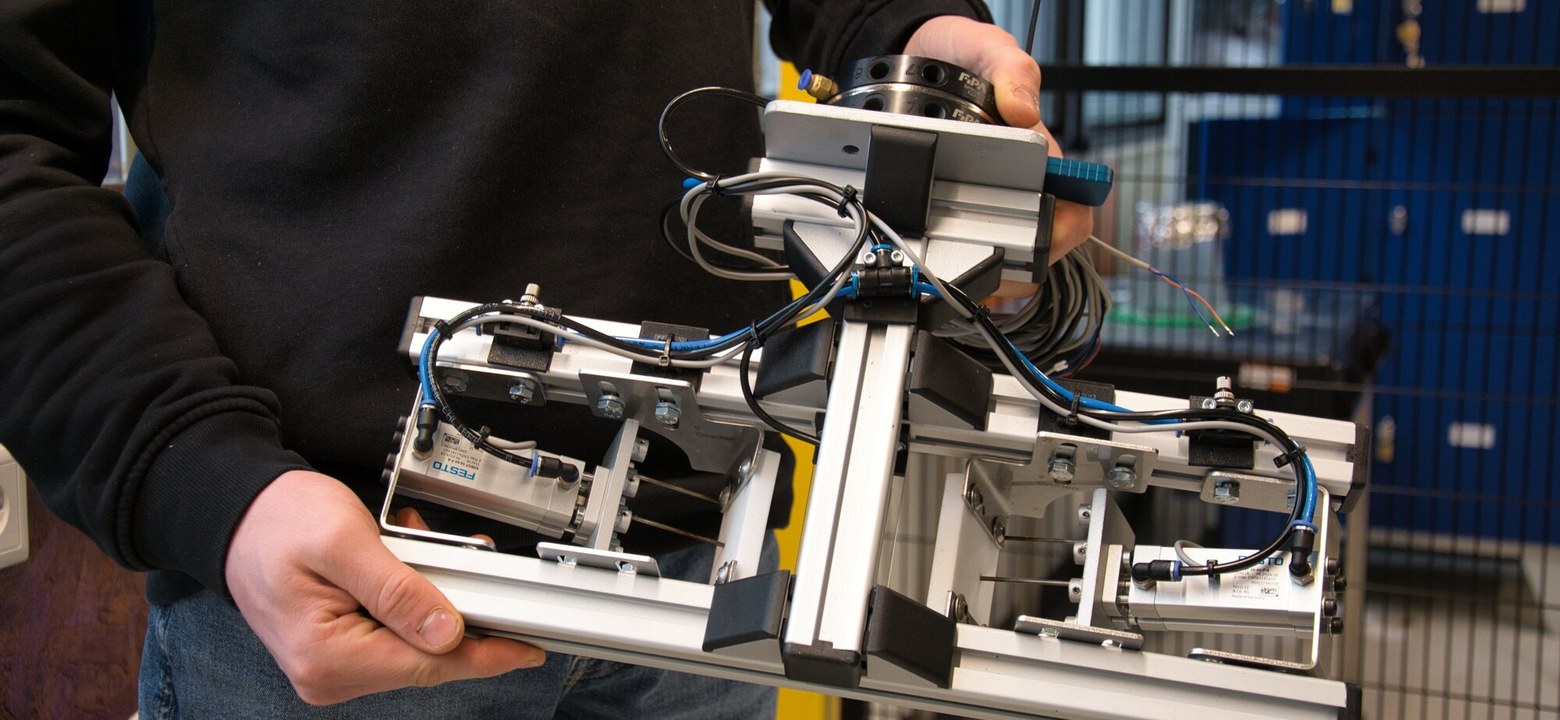
Een collega van Ilse houdt de losgekoppelde LFT handling tool vast.
Van A naar B
Het project rondom de LFT handling tool was mede zo succesvol dankzij de bijdrage van enkele creatieve studenten. Naar welke uitdaging hebben zij precies gekeken? Ilse: “Als de LFT handling tool z’n weg naar de industrie vindt, dan is het dus de bedoeling dat er zo min mogelijk handmatige procestappen nodig zijn. De studenten zijn gaan kijken naar het moment dat het gesmolten materiaal uit de machine komt. Het materiaal wordt dan al gesneden, maar vervolgens moet het nog van A naar B. Hoe zorgen we dat we zoiets stabiel kunnen doen, zonder dat er vervormingen plaatsvinden of dat we temperatuur verliezen?”
Het lijkt toch best al een serieuze technologische uitdaging, zeker voor een groep studenten. “In dit geval ging het om een gevarieerde groep van vijf,” zegt Ilse. “Twee studenten van Mechatronica, twee van Werktuigbouwkunde en één student Elektrotechniek. Ze hadden allemaal een hele productieve houding. Ze zeiden echt: dit is nu ons probleem geworden. Vervolgens maakten ze een taakverdeling, van projectleider tot degene die op de kosten moest letten. Na verloop van tijd kwamen ze bij ons met de eerste ontwerpschetsen. Samen zijn we toen gaan toewerken naar drie onderbouwde concepten, die de projectgroep aan ons lectoraat heeft gepresenteerd.”
Perfect in de mal
Wat het project voor de deelnemende studenten extra leuk maakte, is dat ze konden werken met tastbare resultaten. Bovendien mochten ze hun bevindingen ook presenteren aan praktijkpartners, zoals Fokker en Toray. Waarbij ze zich “goed staande wisten te houden.” Leert Ilse op haar beurt ook nieuwe dingen van de studenten waarmee ze samenwerkt? “Ze hebben ook voor de programmering achter de tool gezorgd,” vertelt ze. “Zodat de machine op elk moment weet waar-ie is. Kijk, ik ben van huis uit een werktuigbouwkundige, met een achtergrond in materialen. Dus wat die studenten laten zien is voor mij dan weer andere koek. Toen hebben ze me stap voor stap meegenomen; dat is een hele leuke manier van samenwerken.”
Terwijl we aan het praten zijn in een projectruimte met uitzicht op allerlei machines, komt er iemand binnengelopen die een stuk gereedschap is vergeten. Het past allemaal bij de laagdrempelige TPAC-cultuur, iets wat er weer voor zorgt dat studenten tijdens projecten met eigen inbreng durven te komen. “Precies,” zegt Ilse. “Zo hebben we tijdens het project onze collega die gespecialiseerd is in mallen er gewoon een keer bij getrokken. Met de vraag wat misschien nog slim is om aan te passen. Zo kom je echt gezamenlijk tot een mooi eindresultaat.”
Foto's Ilse: Thomas Busschers
Meer info over het project Processing of rTPC?
Ga dan naar de projectpagina.