De duurzame belofte van lichtgewicht composieten
Bij het lectoraat Lichtgewicht Construeren vormen vlasvezels de basis voor duurzaam plaatmateriaal, en gaan composiet-tapes van gerecycled kunststof door de weefmachine. Het zijn innovaties in de geest van de Twentse maakindustrie. Recent rondden lector Ferrie van Hattum en zijn collega’s Ilse ten Bruggencate en Rik Brouwer twee innovatie samenwerkingsprojecten af: Rightweight en 3DFlax. In project Rightweight is onder andere een composiet ontwikkeld dat volledig uit gerecycled kunststof bestaat. Binnen het ELIIT-project 3DFlax werd biomateriaal verwerkt tot composiet. Over vlas uit Turkije, lokale makers en een groenere automotive en aerospace industrie.
“Wij zijn een beetje de R&D-afdeling van het midden- en kleinbedrijf in de maakindustrie,” zegt Ferrie van Hattum, lector Lichtgewicht Construeren. “Als je een klein bedrijf bent, kun je je duurste mensen niet een half jaar lang alleen maar onderzoek laten doen. Dus die taak nemen wij van ze over. Op die manier is het Rightweight-project ook ontstaan.”
Hoewel de Nederlandse economie niet wordt gekenmerkt door grootschalige productie van voertuigen, is er wel een innovatieve maakindustrie; iets wat je onder andere terugziet in het midden- en kleinbedrijf van Oost-Nederland. De vraag wat innovatieve makers in het mkb kunnen betekenen voor de automotive of aerospace industrie, vormde de aanleiding voor het Europese project Rightweight, waarin het lectoraat Lichtgewicht Construeren penvoerder is. Ferrie vertelt: “We hebben eindgebruikers gevraagd: op welke technologieën zitten jullie te wachten? De vraagstukken die we terugkregen hebben we vervolgens uitgezet bij het midden- en kleinbedrijf van de deelnemende landen, en die bedrijven konden zich daarop inschrijven met oplossingen.”
Green Deal
Projecten Rightweight en 3DFlax zijn in lijn met de Europese Green Deal, waarin beleid is geformuleerd dat moet leiden tot een klimaatneutraal Europa in 2050; in 2030 moet de CO2-uitstoot tenminste 55% zijn teruggedrongen ten opzichte van 1990.
De ‘thuisbasis’ voor beide projecten was het ThermoPlastic composites Application Center (TPAC) van Saxion, waarbinnen het lectoraat Lichtgewicht Construeren samenwerkt met haar partners.
Een van de eerste en belangrijkste stappen is dan de overgang van op olie gebaseerde kunststoffen naar gerecyclede kunststoffen.
Groene maakindustrie
De maakindustrie is zichzelf momenteel aan het ‘vergroenen’. Bedrijven in die sector zien dat hun klanten aan steeds meer eisen op het gebied van duurzaamheid moeten voldoen. Het gebruik van een materiaal als kunststof staat daarom steeds meer onder druk. “Tegenwoordig is de productie nog op aardolie gebaseerd,” licht Ferrie toe. “Dat is ook onderdeel van het milieuprobleem: het duurt wel heel lang voordat kunststof weer door de natuur is afgebroken.” De noodzaak voor verduurzaming, vertaalt zich voor de maakindustrie naar verwachting in een soort ‘CO2-paspoort’. Hierin moet aan het eind van een productieketen duidelijk worden hoe groot de CO2-uitstoot was. Ferrie: “Een van de eerste en belangrijkste stappen is dan de overgang van op olie gebaseerde kunststoffen naar gerecyclede kunststoffen.
Precies dat was een van de uitdagingen binnen Rightweight. De kennis om een dergelijke uitdaging aan te gaan, is aanwezig binnen verschillende industrieën. “Rightweight probeerde een connectie te maken tussen automotive en aerospace,” vertelt Ilse ten Bruggencate, onderzoeker Lichtgewicht Construeren. “Beide industrieën excelleren op een ander punt. Aerospace is heel ver met hightech materialen en automotive is weer goed in snelle en grote productie. Het idee was om kennis van beide partijen onderling te delen. Om automotive verder te helpen met materialenkennis en aerospace met die productiesnelheid.”
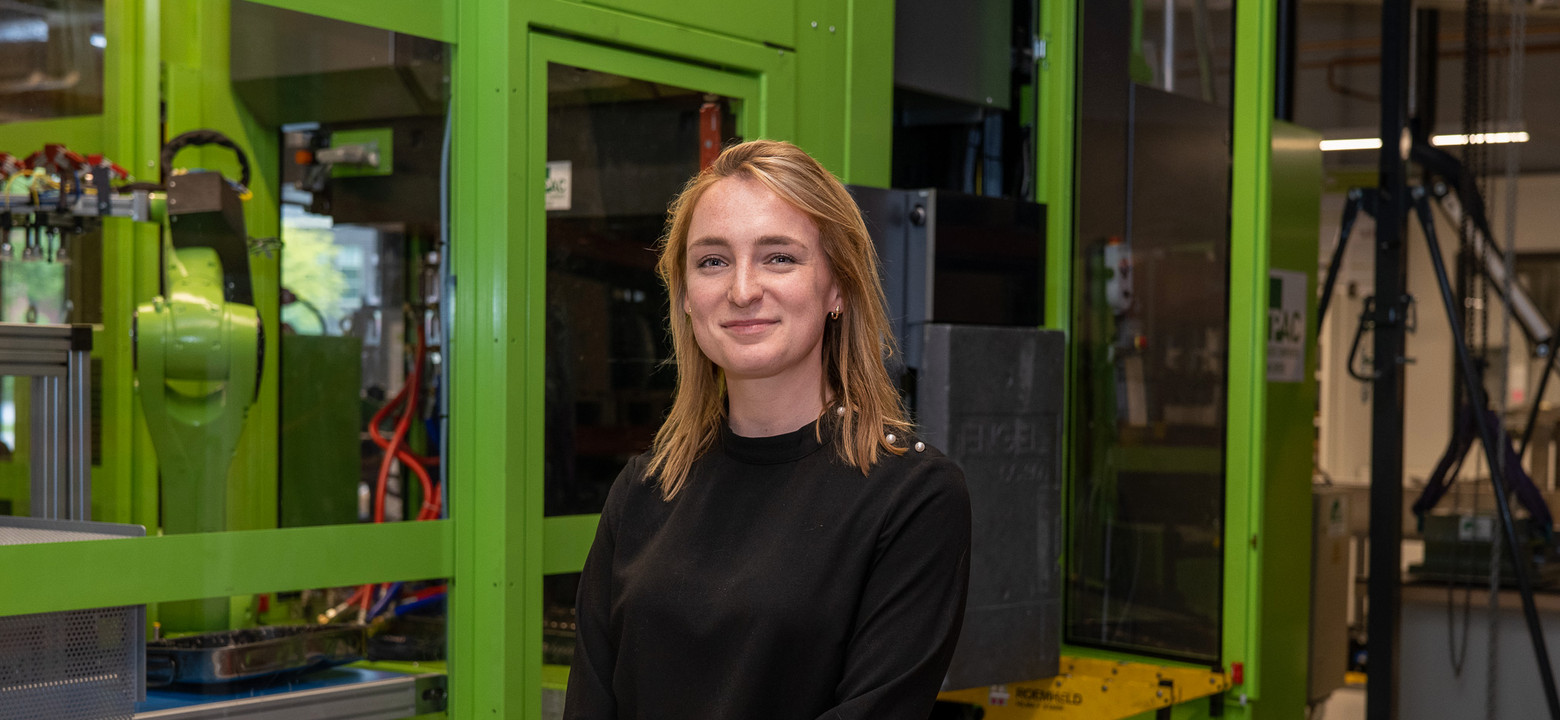
Ilse ten Bruggencate, onderzoeker Lichtgewicht Construeren, bij een spuitgietmachine in TPAC.
Hoe zet je de eerste stappen als het gaat over de productie van gerecycled kunststof op grote schaal? Een van de stappen die Ilse heeft gezet, was het aangaan van een samenwerking met de Enschedese startup SPIRAL: “Zij hebben samen met ons onderzoek gedaan naar het recyclen van een vliegtuigafvalstroom, en hoe je daar spuitgietgranulaat van kunt maken. We zitten nu echt in de eerste ontwikkelingsfase. Het doel is om het van lab naar productie te krijgen, en te bewijzen wat de mogelijkheden van het materiaal zijn. Eindgebruikers moeten uiteindelijk hun klanten overtuigen van de mogelijkheden van het recyclaat. Vanaf daar zet je weer de volgende stap.”
Booming business
“Thermoplastische composieten zijn behoorlijk in ontwikkeling,” benadrukt Ferrie. “Er zijn al onderdelen van gemaakt in de aerospace industrie. De automotive industrie begint het ook steeds meer te gebruiken voor dragende delen, en overige industrieën gaan in het kielzog mee. Die wachten tot het allemaal rijp is voor de markt. Maar de eerste echt grote toepassingen mag je dus verwachten in de aerospace en automotive industrie.” In dat verband noemt Ferrie Stellantis, een automotive multinational die bijdraagt aan de fabricage van veertien automerken. “Automotive partijen lopen aan tegen de milieueisen die er vanaf 2030 aan zitten te komen vanuit Europa,” zegt Ferrie. “De helft van je materialen moet tegen die tijd uit eigen afvalstromen komen. Met een materiaal als staal, dat qua mogelijkheden al tegen z’n grenzen aanloopt, wordt het heel moeilijk om bij het recyclen nog te voldoen aan de eigenschappen die nodig zijn voor de auto's van de toekomst. Denk aan elektrische auto’s: hoe lichter, hoe beter.”
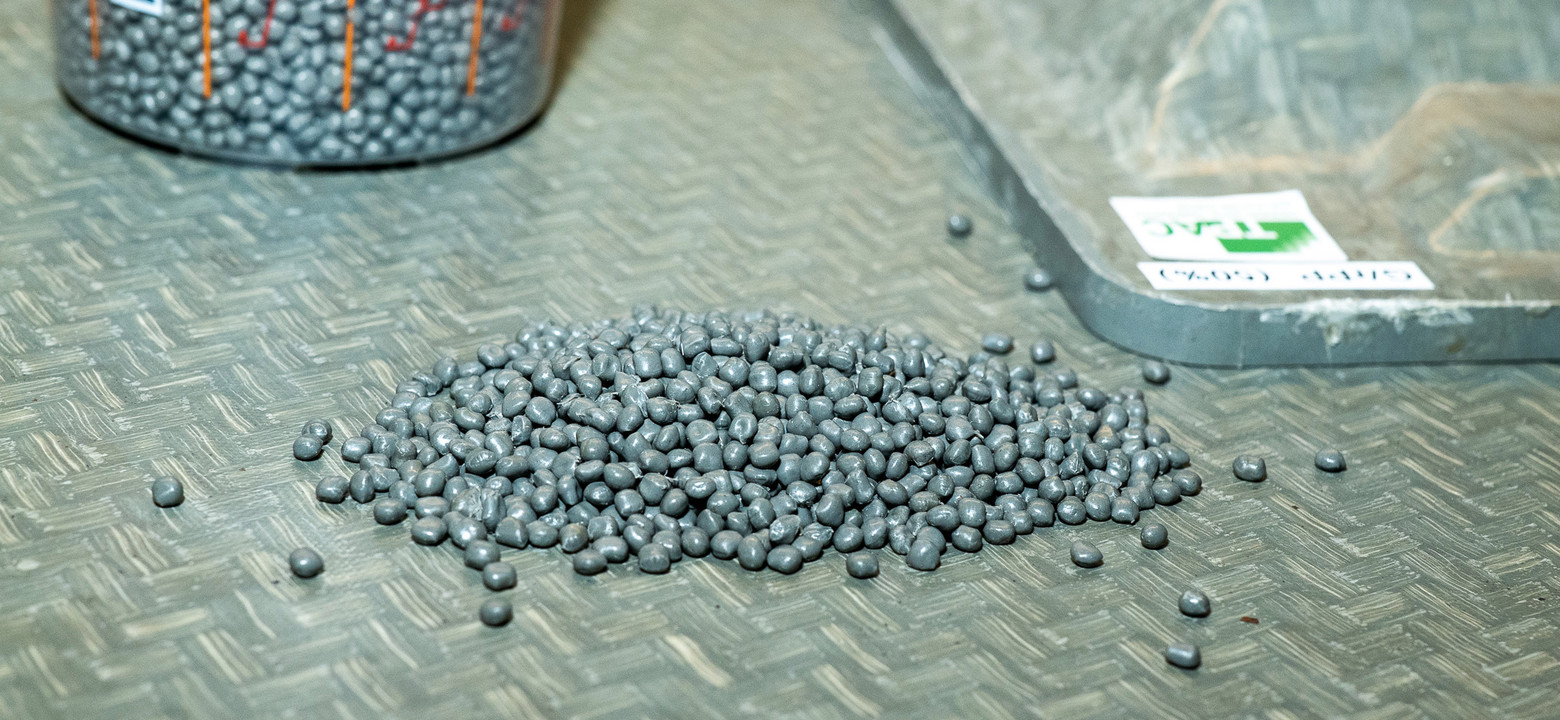
Korrels die zijn gemaakt van post-consumer recyclaat (gebruikt binnen een van de Rightweight-projecten).
Daarom wordt in de automotive industrie de focus langzaam maar zeker verlegd naar het gebruik van composieten. “Er zijn grote bedrijven in Nederland die al een constante stroom kunststofkorrels kunnen leveren,” zegt Ferrie. “Bijvoorbeeld gemaakt van shampooflesjes of ander kunststofafval. We hebben daar vezel-versterkte composiettapes van gemaakt, samen met het Nederlandse bedrijf CompTape. En voor die tapes hebben we weeftechnologie ontwikkeld, want die was nog niet beschikbaar op een betaalbare manier. Zo zijn we tot de eerste demonstrators gekomen.” Met ‘weeftechnologie’ verwijst Ferrie naar een speciale weefmachine, waarin tapes van gerecycled kunststof kruislings tot matten worden geweven, wat voordelen oplevert wat betreft de verwerkbaarheid. Deze matten kunnen weer worden geperst tot hoogwaardige composietplaten. “Vanuit die platen konden we onderdelen maken,” vervolgt Ferrie. “Die onderdelen hebben we op kleine schaal laten zien aan Stellantis als eindgebruiker.” Dit leidde tot een enthousiaste reactie en de verdere ontwikkeling van een demonstrator specifiek voor de automotive industrie.
Geen glasvezel, maar vlásvezel
“Bij 3DFlax gaat het over biocomposiet,” vertelt Rik Brouwer, hoofdocent en onderzoeker Lichtgewicht Construeren. “Biocomposiet is echt een nieuw materiaal, dat zijn weg nog moet vinden.” Binnen het ELIIT-project is een 3d-printtechnologie ontwikkeld waarmee natuurlijke vezeldraden in iedere gewenste figuur kunnen worden ‘neergelegd’. Dit met het doel om tot zo sterk mogelijk composietmateriaal te komen, dat bloot kan staan aan grote krachten. “Wat je ziet,” zegt Rik, “is dat biocomposiet zijn toepassingen met name vindt waar extra eisen ten aanzien van het milieu worden gesteld.” En hoe staat het met biocomposiet in vergelijking tot bestaande, hoogwaardige vezelmaterialen? Rik: “Met bepaalde biocomposieten kun je constructief heel ver komen, dan kom je echt in de buurt van glasvezels. Het gaat dan vooral om vlásvezels, die zijn qua prestaties het beste. Alleen is de vlasindustrie op dit moment nog niet zover. Daar zijn ze nog gefocust op het produceren van linnen.”
Ferrie vult aan: “Aan die kant van het spectrum – de biomaterialen – zijn nog weinig grondstoffen beschikbaar. Een van de weinige partners in ons netwerk die daarmee kunnen helpen, is het kleine Turkse bedrijf BPreg. Eigenlijk een startup nog. Het ELIIT-project was er bewust op gericht om kleinere bedrijven een zetje in de goede richting te geven. Samen met BPreg hebben we de beschikbare grondstoffen op zo’n manier verbeterd dat we ze goed in onze processen kunnen gebruiken. Wij zijn echt die schakel tussen eindgebruikers en kleinere bedrijven.”
Fotografie: Thomas Busschers